LiDAR Production Calibration & Test
High Volume Manufacturing (HVM) Testing Line
About the cooperation
The collaborative project between Konrad and Innoviz has led to the development of an automated test line for lidar devices, consisting of seven specialized stations, which allows for comprehensive calibration and end-of-line testing of highly innovative lidar sensing devices for the automotive industry.
The main reason why Innoviz has choosen Konrad Technologies as project partners was the proven technical expertise in Optics, Automation & Testing as well as the global support capabilities of Konrad having direct branches in Europe, Americas and Asia.
Project Scope
Challenges:
- Main challenge was that any deviations during the alignment process could affect the test results and require additional readjustments which would result into tremendous additional costs during production as well as delayed shipment to end customers.
- In technical terms we had to achieve high precision with an overall tolerance of ±0.03° in pitch, roll, and yaw, ensuring accurate testing results and to maintain exceptional repeat accuracy of ±0.015° in pitch, roll, and yaw for both the DUT and the carrier, enhancing reliability in measurements.
Objectives:
- The goal of the project was to develop a high-precision alignment process of the DUT (Device under Test) with the carrier as well as the machinery and automation.
- During the project it was also a goal to stay flexible and to adapt to new technologies: Lidar technology is evolving rapidly. The test line under development had to be flexible enough to accommodate future adaptations and new test requirements.
Solution
In collaboration with Innoviz, Konrad Technologies has developed an automated test line for lidar devices, featuring 7 Specialized stations designed for comprehensive end-of-line testing. This innovative solution streamlines the testing process, ensuring accuracy and efficiency in the calibration of lidar technologies.
The system provides a conveyor transfer section, lifting out of the section, RF communication, optical test, laser calibration, precise repeat accuracy mechanisms in contacting the DUT.
A wide range of technologies were involved during this Project but key were the accurate alignment technology, high precision measurement, automation expertise, as well as implementing specific RF connection technology in the automotive industry (H-MTD).
It was a calibration and Test Line for the final lidar product so key test items were EOL (end of Line product test) and Flash.
To keep maintaining the high repeat accuracy kept beeing a challenge during project deployment. Only through accurate mechanical work and software optimization by the technical experts from Konrad and a highly productive collaborative work with the Innoviz team made it possible to maintain the high accuracy requirements.
Stations
In the Bring-up Station, the DUTs are energized and an initial Software test is carried out. The Management Station then checks the laser grid with high precision and automatically readjusts it if necessary. In the Laser Station, an Ulbricht sphere validates the wavelength and intensity of the laser.
The Confidence Station simulates strong backlight through static targets and various lighting techniques to test the reliability of the data under poor conditions. In the Parasitic Station, contamination of the viewing panel by moving targets is simulated. In the Distance Station, deviations from the laser are precisely detected at distances of up to 50 meters.
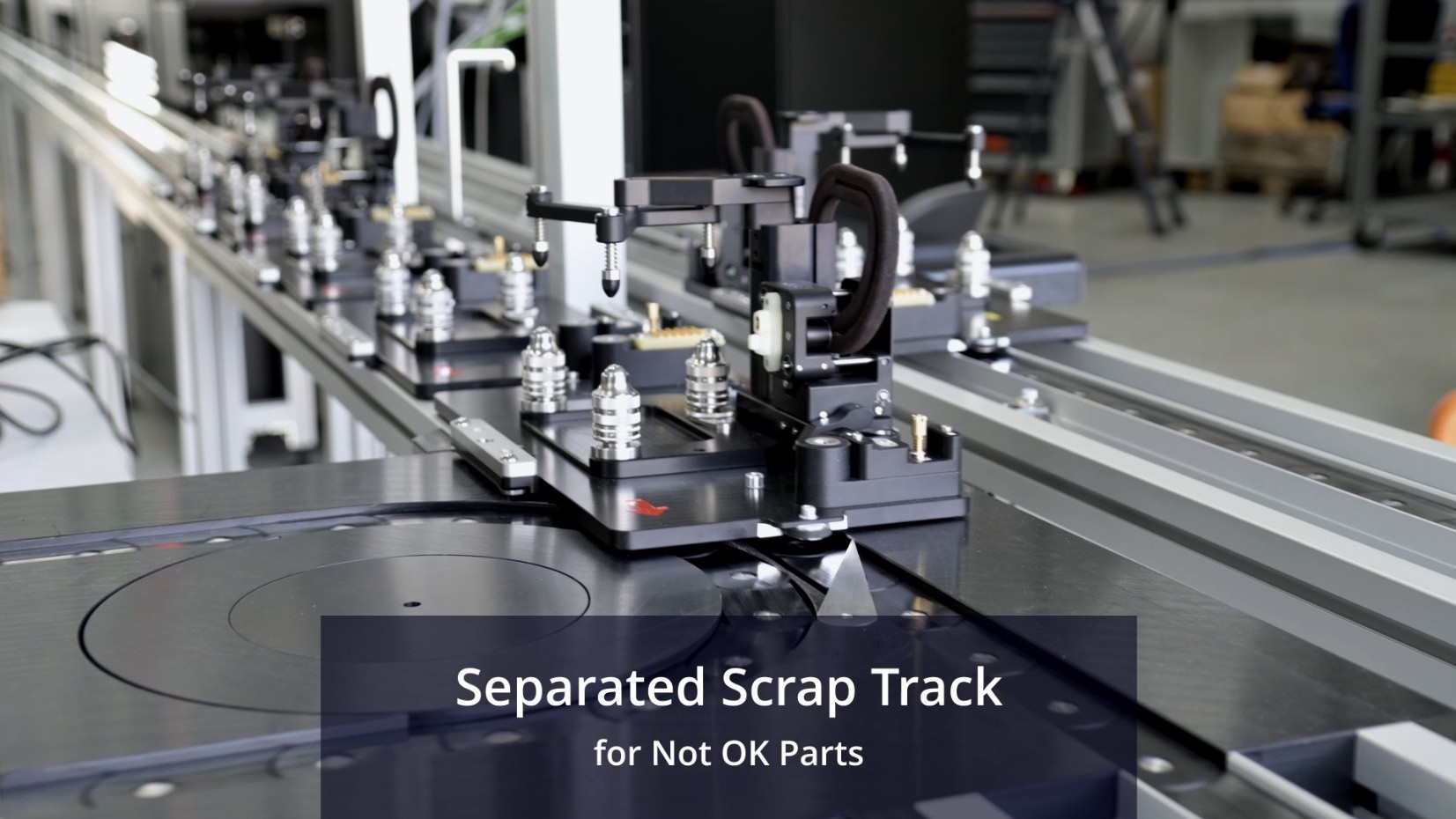
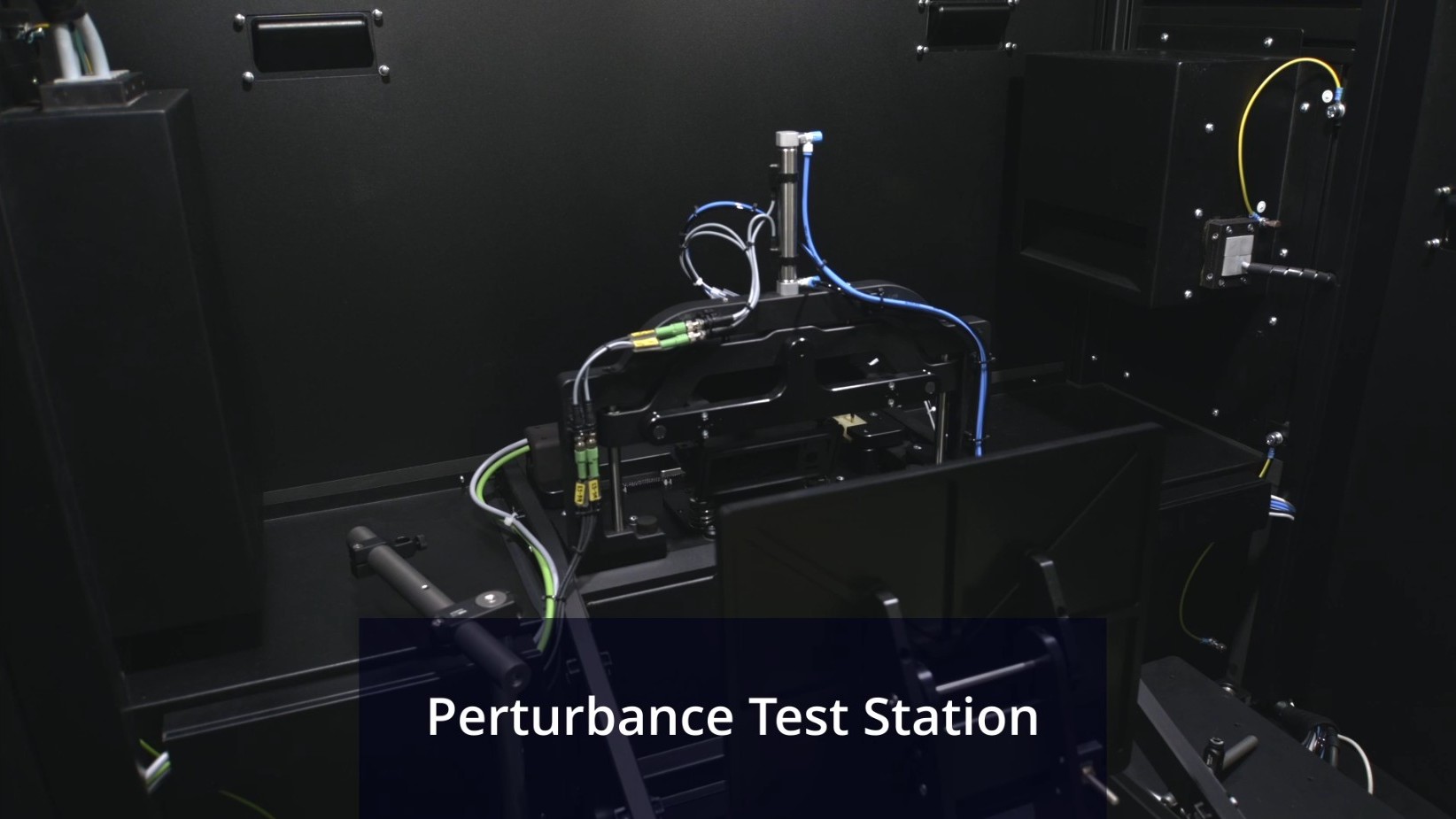
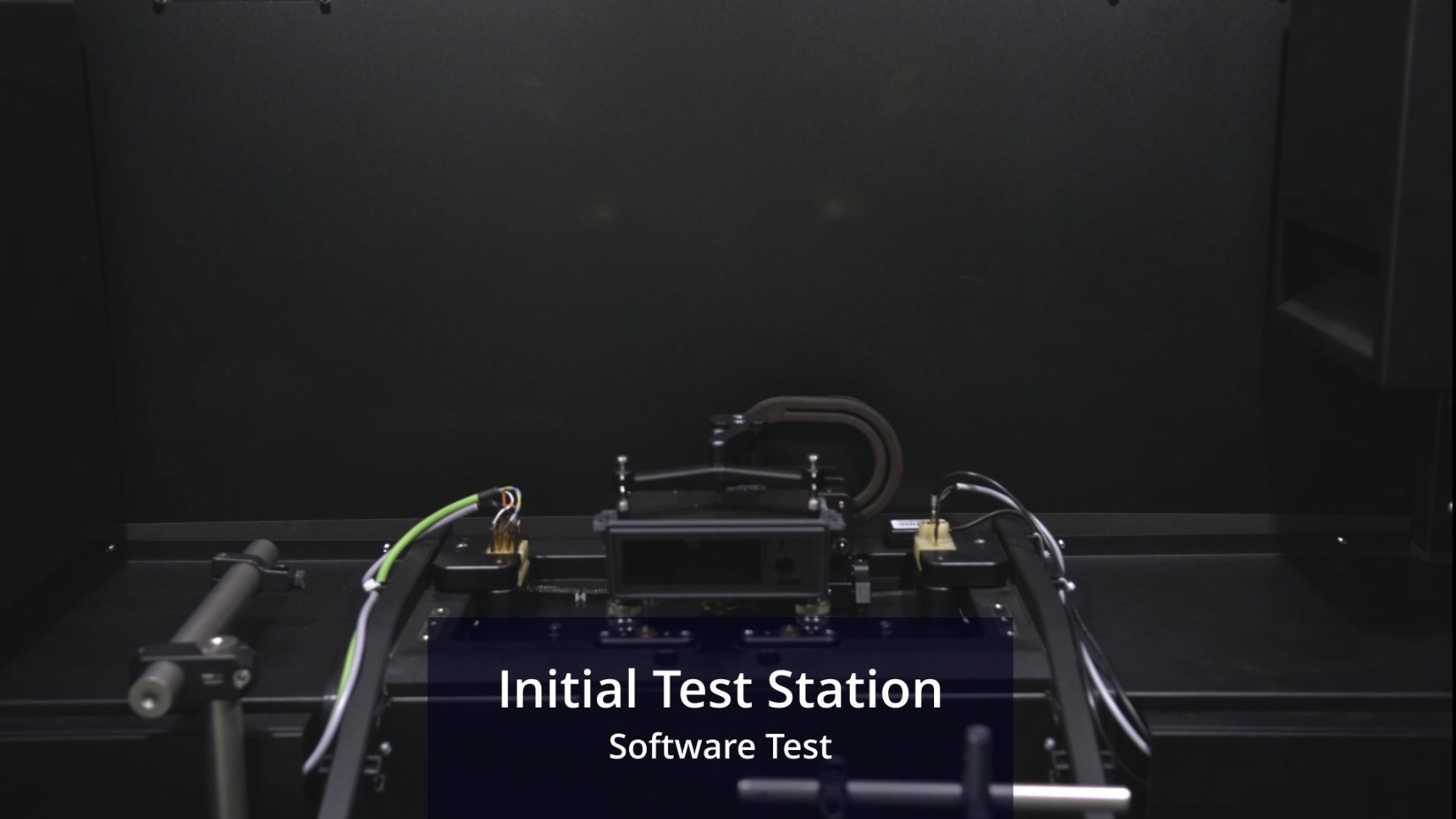
Customer Benefit
Key value for the customer is that the line could meet its expected cycle time, while maining the challenging accuracy requirements. Last but not least to have a reliable service team around the world ready to support customers globally and thus guarantee a fast response time is very valuable to deliver best in class products to their end-customers with the right quality on time.
The new Lidar Production Calibration & Test line created by Konrad and Innoviz is a highly precise machine which was a Pilot project. Major advantages are:
- Short Cycle Time: Achieved a cycle time of just 4 minutes, optimizing throughput and efficiency.
- High-Frequency Measurement Techniques: Employed advanced HF measurement methods to enhance precision and ensure reliable testing outcomes.
- Exceptional Repeat Accuracy: Designed the system to maintain high repeat accuracy throughout the testing process, ensuring consistent and reliable results.
- Vibration Isolation: Implemented a vibration-isolated measuring table, minimizing interference from the circulation belt and surrounding system to enhance measurement precision.
Our know-how for project implementation
The collaborative work between technical experts in RF technology, optics, electrial design, high precision mechanical design and manufacturing as well as open communication with technical experts at customer site enabled us to deliver this highly complex line successfully. Only through team work between different technology sectors such complex machinery can be developed.
your project!
Let us know what you're working on and how we can help you get there
through our long term experience in large high tech projects.